The taste of cocoa powder and the solidity of cement are just a couple of examples of how particle size can have a significant impact on a product’s chemical and physical properties.
Knowing a material’s particle size distribution—and the effects of altering it—plays a crucial role in the quality control process for any industrial product. Due to the high level of accuracy, low investment cost, and ease of handling, vibratory screening is among the most commonly used methods for targeting a product’s particle size.
Whether it’s being used for product development, production control, or as quality control for another service entirely (ball milling, spray drying, or roll drying for example), vibratory screening is a proven technique for delivering consistent, reliable throughputs.
That’s why, when a customer came to us with a specialized industrial material that required a particle size modification, we knew vibratory screening would be the right process to use.
What is vibratory screening?
Vibratory screening, also known as mechanical screening, is the process of taking particulate material and separating it into multiple grades by particle size. This method of particle separation uses gravity, motion, and mesh screens to accomplish the separation. A series of screens can be set up to allow for multiple size classifications in one pass.
The screener itself is mechanically vibrated in a controlled manner to allow the particles to flow across the screen and outward in a spiral pattern. The oversize particles flow across the screen and are discharged through a spout. Any fine particles fall through the mesh screen(s) and continue to spiral until they are discharged.
AVEKA has several models and sizes (ranging from 8”- 60” diameter) of vibratory screeners, which we use to classify a broad range of dry materials, including:
- Polymers
- Pigments
- Oxides
- Inorganics
- Organics
- Food
In addition, AVEKA has ultrasonic screeners and air classification systems available that more efficiently classify low-density materials.
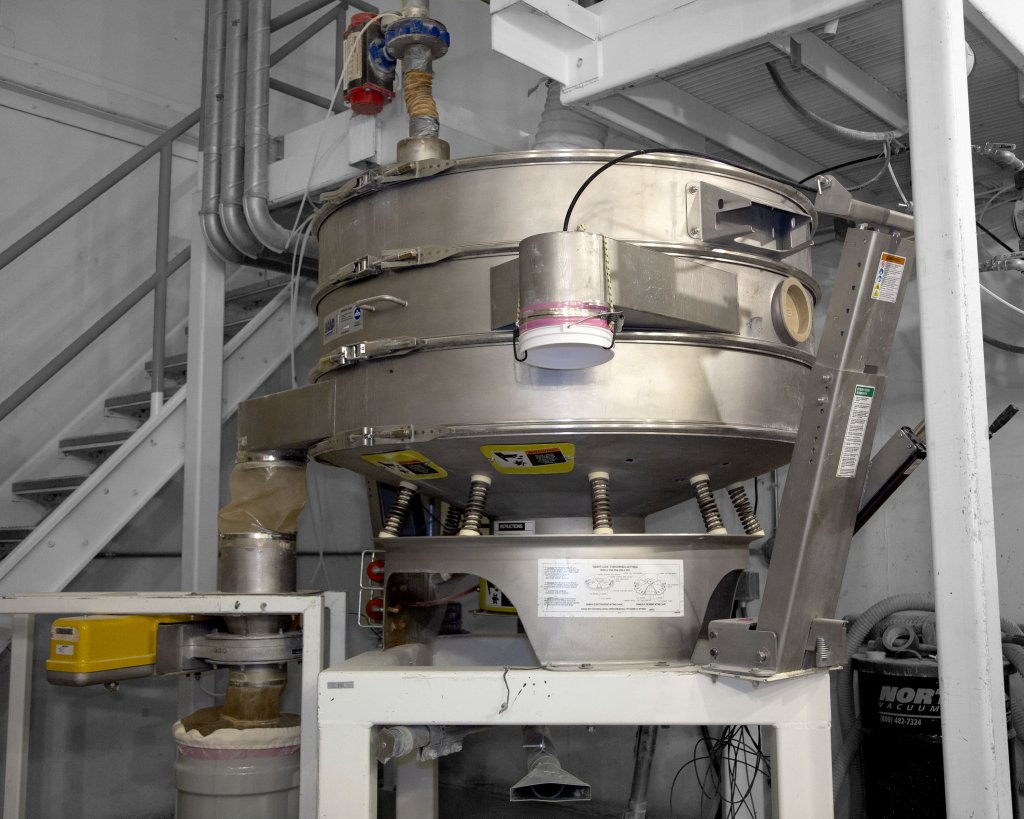
An AVEKA vibratory screener
Screening challenges
The customer came to us with 50 lbs. of their proprietary material. The particle size of the incoming product had a D95 of approximately 500 µm, and they wanted to modify it down to two target particle sizes that would have a D95 of 300 and 350 µm.
This project presented two unique challenges that needed to be addressed:
- The material wasn’t spherical, but rather a jagged, rod-like shape.
- The material itself was deemed high value by the customer.
The AVEKA solution
We began the process with extensive lab-scale testing at our AVEKA Inc. facility in Woodbury, Minnesota. After numerous laboratory screen size tests, we were able to determine the two optimal screen sizes needed for our production screener: an 80 mesh and a 105 tensile bolt cloth. These two screens allowed us to reach the optimal D95 ranges.
To counteract the issue with the rod-like shape of the particles, we had to adjust our typical solution and go with a slightly smaller screen size. We also introduced bouncing balls and sliding disks during our runs to encourage more particle movement across the screens.
Since the material was considered high value, we were careful not to incur any unnecessary waste throughout the process. All oversized particles were either re-screened or sent back to the customer, and any fine particles were collected and returned as well.
Particles within the target range were thoroughly tested in our in-house characterization lab to verify they met the customer’s requirements. Once they passed the quality control testing, they were packaged into appropriately sized lined containers and shipped to the customer.
Screen your products with AVEKA
With over 20 years of experience, AVEKA is your one-stop-shop for material processing and classification services. We offer high screening throughput, great product quality, and low wear on your materials. Contact us today to discuss your unique needs.